数控技术作为现代制造业的核心技术,通过数字化控制实现精密加工与自动化生产。本文将深入解析其核心功能、技术原理及行业应用,并结合实际案例与趋势展望,为从业者提供实用建议。
一、数控技术的核心功能与工作原理
1. 数字化控制的本质
数控技术以数字信号为基础,通过编程指令控制机床运动轨迹、速度及加工参数。其核心功能包括:
精准定位:通过伺服系统与反馈装置(如光栅尺)实现微米级精度控制。
多轴联动:支持三轴至五轴联动加工,适用于复杂曲面零件(如航空发动机叶片)的制造。
自动化流程:集成自动换刀、在线检测等功能,减少人工干预。
2. 技术架构与工作流程
典型数控系统由三大部分组成:
1. 硬件层:包括控制器(如多核处理器)、伺服驱动单元、机床本体及传感器。
2. 软件层:涵盖操作系统(如定制Linux内核)、编程软件(支持G代码/M代码)及模拟工具。
3. 数据接口:通过以太网、OPC UA等协议实现设备互联与远程监控。
工作流程示例:编程输入→指令解析→伺服驱动→实时反馈→加工完成。
二、数控技术的行业应用与典型案例
1. 机械制造与汽车工业
复杂零件加工:五轴联动技术用于加工汽车变速箱壳体,效率比传统工艺提升40%。
柔性生产线:数控机床与工业机器人协同作业,实现汽车零部件的混线生产。
2. 航空航天与精密仪器
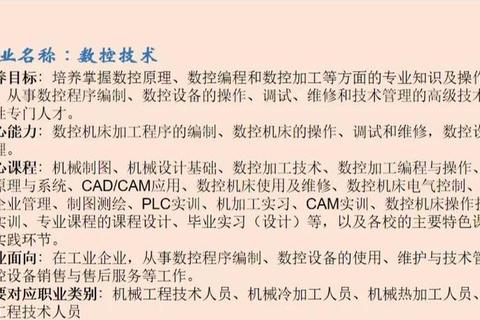
钛合金加工:高速铣削技术解决航空材料的高硬度、低导热性难题,表面粗糙度可达Ra0.4μm。
卫星部件制造:纳米级数控机床用于光学元件的超精密加工。
3. 模具制造与医疗器械
注塑模具:数控电火花加工(EDM)实现微细孔加工,精度达±0.005mm。
骨科植入物:个性化定制假体通过数控切削完成,匹配患者骨骼结构。
三、行业面临的挑战与应对策略
1. 技术瓶颈
高端设备依赖进口:五轴机床、高精度主轴等核心部件仍依赖德国、日本技术。
软件生态不完善:国产CAM软件在算法优化与兼容性上存在差距。
2. 人才培养与成本控制
技能缺口:预计2025年我国数控领域高技能人才缺口达450万。
解决方案:
校企合作:建立实训基地(如安庆职院的智能制造实训室)。
模块化培训:分阶段掌握编程、操作与维护技能。
四、未来发展趋势与创新方向
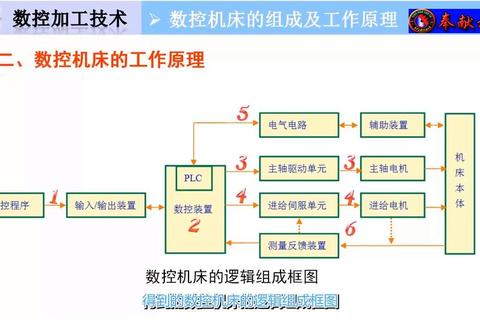
1. 智能化与集成化
AI工艺优化:机器学习算法自动匹配切削参数,减少试错成本。
数字孪生:通过3D仿真预判加工误差,优化生产流程。
2. 绿色制造与微型化
能耗优化:动态功率调整技术降低机床待机能耗30%。
桌面级设备:微型数控机床满足创客与小批量生产需求。
五、从业者的实用建议
1. 技能提升路径:
初阶:掌握数控车/铣床操作,考取数控车工中级证书。
进阶:学习CAD/CAM软件(如NX)、五轴编程与设备维护。
2. 技术选型指南:
中小批量生产优选加工中心,大批量场景适用柔性制造单元(FMC)。
关注支持物联网的数控系统(如海德汉iTNC530),便于远程监控。
3. 职业发展资源:
参与行业竞赛(如全国数控技能大赛)积累实战经验。
关注《制造业人才发展规划指南》等政策导向,把握新兴领域机会。
数控技术正从“精密工具”向“智能制造中枢”演变。企业需加快技术升级与人才储备,个人则应注重跨领域技能融合(如编程+工艺分析),方能在产业变革中抢占先机。通过持续创新与生态协作,数控技术将推动制造业迈向更高效、智能的未来。